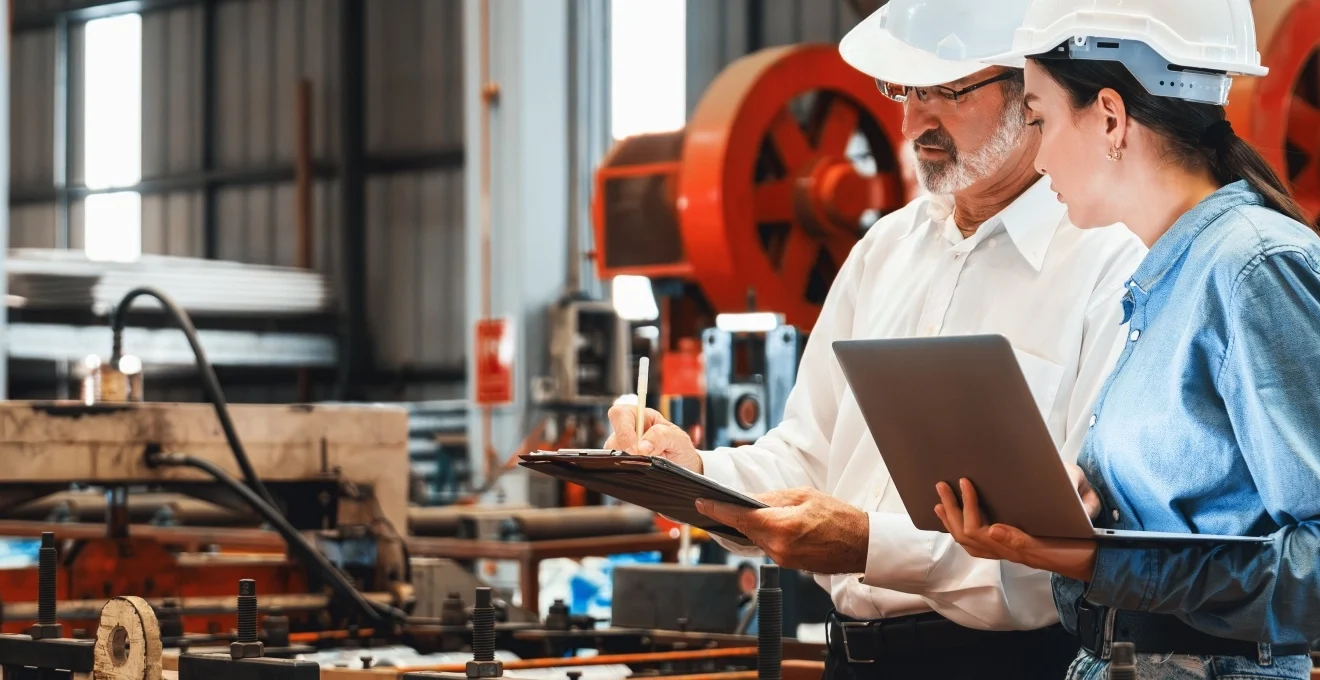
L'optimisation des processus industriels est un enjeu crucial pour toute entreprise cherchant à maximiser sa rentabilité. Dans un environnement économique de plus en plus compétitif, la capacité à produire de manière efficace et à moindre coût peut faire toute la différence. L'amélioration continue des méthodes de production, l'adoption de nouvelles technologies et la rationalisation des opérations sont devenues essentielles pour rester performant. Cette quête d'excellence opérationnelle nécessite une approche globale, alliant analyse pointue des processus existants, intégration judicieuse des innovations technologiques et optimisation de la chaîne logistique, en s'appuyant sur des matériels et solutions industrielles performants.
Analyse des processus industriels actuels
La première étape pour améliorer la rentabilité d'un processus industriel est de réaliser un audit complet des opérations existantes. Cette analyse approfondie permet d'identifier les goulots d'étranglement, les inefficacités et les opportunités d'optimisation. Il est crucial d'examiner chaque étape du processus de production, depuis l'approvisionnement en matières premières jusqu'à la livraison du produit fini.
Pour mener à bien cette analyse, plusieurs outils et méthodologies peuvent être utilisés. La cartographie des flux de valeur (VSM - Value Stream Mapping) est particulièrement efficace pour visualiser l'ensemble du processus et repérer les zones d'amélioration potentielles. Cette technique permet de mettre en évidence les temps d'attente, les stocks intermédiaires excessifs et les étapes n'apportant pas de valeur ajoutée.
L'analyse des données de production est également essentielle. Les systèmes MES (Manufacturing Execution System) fournissent des informations précieuses sur les performances des équipements, les temps de cycle et la qualité des produits. Ces données permettent d'identifier les machines les moins performantes, les causes récurrentes d'arrêts de production et les variations de qualité.
Une analyse approfondie des processus actuels est le fondement de toute démarche d'amélioration. Sans une compréhension claire de l'existant, il est impossible de définir des objectifs d'optimisation pertinents et réalistes.
Il est également important d'impliquer les opérateurs et les superviseurs dans cette phase d'analyse. Leur expérience quotidienne du terrain est une source précieuse d'informations sur les difficultés rencontrées et les pistes d'amélioration potentielles. Des séances de brainstorming et des groupes de travail peuvent être organisés pour recueillir leurs idées et suggestions.
Technologies d'automatisation avancées
L'automatisation joue un rôle crucial dans l'amélioration de la rentabilité des processus industriels. Les technologies modernes permettent d'accroître la productivité, de réduire les erreurs humaines et d'optimiser l'utilisation des ressources. Parmi les solutions les plus prometteuses, on trouve les systèmes de contrôle distribué, les automates programmables industriels et les applications d'intelligence artificielle, le tout reposant sur des matériels et solutions industrielles de pointe.
Systèmes de contrôle distribué (DCS)
Les systèmes de contrôle distribué (DCS) sont des plateformes intégrées permettant de piloter et de superviser l'ensemble d'un processus industriel. Ils offrent une vue globale des opérations et permettent une gestion centralisée des différents équipements. Les DCS modernes intègrent des fonctionnalités avancées telles que :
- La régulation adaptative pour optimiser les paramètres de production en temps réel
- La gestion prédictive de la maintenance pour réduire les temps d'arrêt
- L'analyse avancée des données pour identifier les opportunités d'amélioration
- L'intégration avec les systèmes de gestion de l'entreprise (ERP, MES, etc.)
Automates programmables industriels (API)
Les automates programmables industriels (API) sont au cœur de l'automatisation des processus de production. Ces dispositifs robustes et flexibles permettent de contrôler avec précision les équipements industriels. Les API modernes offrent des capacités de traitement accrues et des fonctionnalités avancées, telles que :
- La communication en temps réel avec d'autres systèmes via des protocoles industriels standards
- L'intégration de modules de sécurité pour une meilleure protection des opérateurs et des équipements
- La possibilité de programmer des algorithmes complexes pour optimiser les processus
- La visualisation et le diagnostic à distance pour une maintenance facilitée
L'utilisation d'API performants permet d'accroître la flexibilité des lignes de production et de réduire les temps de changement de série. Une entreprise du secteur automobile a ainsi pu augmenter sa productivité de 25% en modernisant ses systèmes d'automatisation basés sur des API.
Intelligence artificielle et apprentissage automatique
L'intelligence artificielle (IA) et l'apprentissage automatique ouvrent de nouvelles perspectives pour l'optimisation des processus industriels. Ces technologies, souvent intégrées aux matériels et solutions industrielles modernes, permettent d'analyser de grandes quantités de données pour identifier des patterns complexes et prendre des décisions en temps réel. Parmi les applications prometteuses, on peut citer :
- L'optimisation dynamique des paramètres de production en fonction des conditions réelles
- La détection précoce des anomalies et la prédiction des pannes
- L'amélioration de la qualité des produits grâce à des contrôles visuels automatisés
- L'optimisation de la planification de la production et de la gestion des stocks
L'adoption de technologies d'automatisation avancées n'est pas une option, mais une nécessité pour les entreprises souhaitant rester compétitives dans un environnement industriel en constante évolution.
Optimisation de la chaîne d'approvisionnement
Une chaîne d'approvisionnement efficace est essentielle pour améliorer la rentabilité d'un processus industriel. L'optimisation de la logistique permet de réduire les coûts, d'améliorer la réactivité face aux fluctuations du marché et d'assurer une meilleure satisfaction des clients. Plusieurs approches peuvent être mises en œuvre pour atteindre ces objectifs, grâce à l'intégration de matériels et solutions industrielles adaptés.
Gestion des stocks en flux tendu
La gestion des stocks en flux tendu, ou just-in-time, vise à réduire au minimum les niveaux de stocks tout en assurant la disponibilité des matières premières et des composants nécessaires à la production. Cette approche permet de :
- Réduire les coûts de stockage et les risques d'obsolescence
- Améliorer la rotation des stocks et libérer du capital
- Identifier plus rapidement les problèmes de qualité
- Accroître la flexibilité face aux changements de la demande
La mise en place d'une gestion en flux tendu nécessite une collaboration étroite avec les fournisseurs et une excellente maîtrise des délais d'approvisionnement. Des outils de vendor-managed inventory (VMI) peuvent faciliter cette démarche en permettant aux fournisseurs de gérer directement les stocks de leurs clients.
Planification avancée de la production
Les systèmes de planification avancée de la production (APS - Advanced Planning and Scheduling) permettent d'optimiser l'utilisation des ressources en tenant compte de multiples contraintes. Ces outils sophistiqués intègrent des algorithmes d'optimisation pour :
- Équilibrer la charge de travail entre les différentes ressources
- Minimiser les temps de changement de série
- Optimiser les séquences de production pour réduire les gaspillages
- Anticiper les besoins en matières premières et en composants
Traçabilité et suivi en temps réel
La traçabilité des produits et le suivi en temps réel des flux logistiques sont devenus des enjeux majeurs pour les entreprises industrielles. Les technologies telles que la RFID (Radio Frequency Identification) et l'IoT (Internet of Things) permettent de :
- Localiser précisément les produits à chaque étape de la chaîne logistique
- Optimiser les routes de transport et réduire les coûts logistiques
- Améliorer la gestion des retours et des rappels de produits
- Lutter contre la contrefaçon et garantir l'authenticité des produits
Amélioration de l'efficacité énergétique
L'optimisation de la consommation énergétique est un levier majeur pour améliorer la rentabilité des processus industriels. Avec la hausse des coûts de l'énergie et les préoccupations environnementales croissantes, les entreprises ont tout intérêt à mettre en place des mesures d'efficacité énergétique, en choisissant des matériels et solutions industrielles éco-responsables.
Plusieurs approches peuvent être adoptées pour réduire la consommation d'énergie :
- L'installation de systèmes de récupération de chaleur pour valoriser l'énergie thermique perdue
- L'optimisation des process de production pour réduire les pertes énergétiques
- L'utilisation de moteurs et d'équipements à haut rendement énergétique
- La mise en place de systèmes de gestion de l'énergie (SGE) pour un pilotage fin de la consommation
Les systèmes de gestion de l'énergie basés sur la norme ISO 50001 permettent une approche structurée de l'amélioration de la performance énergétique. Ces systèmes intègrent des fonctionnalités telles que :
- Le monitoring en temps réel de la consommation d'énergie
- L'identification des sources de gaspillage énergétique
- La définition et le suivi d'indicateurs de performance énergétique (IPE)
- La mise en place de plans d'action pour réduire la consommation
Méthodologies Lean et Six Sigma
Les méthodologies Lean et Six Sigma sont des approches complémentaires visant à améliorer la performance des processus industriels. Le Lean se concentre sur l'élimination des gaspillages et la création de valeur pour le client, tandis que le Six Sigma vise à réduire la variabilité des processus et à améliorer leur qualité. L'application de ces méthodologies est souvent facilitée par l'utilisation de matériels et solutions industrielles appropriés.
Cartographie de la chaîne de valeur
La cartographie de la chaîne de valeur (VSM - Value Stream Mapping) est un outil fondamental du Lean Manufacturing. Elle permet de visualiser l'ensemble du flux de valeur, depuis la réception des matières premières jusqu'à la livraison du produit fini. Cette technique aide à :
- Identifier les étapes n'apportant pas de valeur ajoutée
- Repérer les goulots d'étranglement et les sources de gaspillage
- Définir un état futur optimisé du processus
- Élaborer un plan d'action pour atteindre cet état futur
La réalisation d'une VSM peut conduire à des améliorations significatives. Une étude de cas dans l'industrie automobile a montré qu'une entreprise a pu réduire son lead time de production de 45% grâce à l'utilisation de cette technique.
Réduction des gaspillages (Muda)
La réduction des gaspillages, ou "Muda" en japonais, est un concept central du Lean Manufacturing. Il vise à éliminer toutes les activités n'apportant pas de valeur ajoutée au produit final. Les 7 types de gaspillages classiques sont :
- La surproduction
- Les attentes
- Les transports inutiles
- Les traitements inutiles ou mal faits
- Les stocks excessifs
- Les mouvements inutiles
- Les défauts et retouches
L'identification et l'élimination systématique de ces gaspillages permettent d'améliorer significativement l'efficacité des processus. Par exemple, une entreprise du secteur électronique a pu réduire ses coûts de production de 20% en mettant en place une démarche de chasse aux gaspillages.
Contrôle statistique des processus
Le contrôle statistique des processus (SPC - Statistical Process Control) est un outil clé du Six Sigma. Il permet de surveiller et de contrôler la variabilité des processus de production. Les principales techniques utilisées sont :
- Les cartes de contrôle pour suivre l'évolution des paramètres critiques
- L'analyse de capabilité pour évaluer la performance des processus
- Les plans d'expériences pour optimiser les paramètres de production
- L'analyse des systèmes de mesure pour garantir la fiabilité des données
Déploiement de la fonction qualité (QFD)
Le déploiement de la fonction qualité (QFD - Quality Function Deployment) est une méthode structurée pour traduire les besoins des clients en spécifications techniques. Cette approche permet de :
- Aligner le développement des produits sur les attentes des clients
- Améliorer la communication entre les différents services de l'entreprise
- Réduire les cycles de développement et les coûts associés
- Augmenter la satisfaction client et la qualité des produits
Maintenance prédictive et IoT industriel
La maintenance prédictive, associée aux technologies de l'Internet des Objets Industriel (IIoT), représente une avancée majeure dans l'optimisation des processus industriels. Cette approche permet de prévenir les pannes avant qu'elles ne se produisent, réduisant ainsi les temps d'arrêt et les coûts de maintenance. L'efficacité de la maintenance prédictive repose souvent sur l'intégration de matériels et solutions industrielles spécifiques.
Les principales composantes d'un système de maintenance prédictive basé sur l'IIoT sont :
- Des capteurs intelligents pour collecter des données en temps réel sur l'état des équipements
- Des plateformes de gestion des données pour centraliser et analyser les informations
- Des algorithmes d'intelligence artificielle pour prédire les défaillances potentielles
- Des interfaces utilisateurs pour visualiser les informations et planifier les interventions
La combinaison de la maintenance prédictive et de l'IIoT permet non seulement d'optimiser les coûts, mais aussi d'améliorer la sécurité et la qualité des produits en garantissant un fonctionnement optimal des équipements.
En outre, l'IIoT offre de nouvelles possibilités pour optimiser l'ensemble du processus de production. Par exemple, la collecte et l'analyse en temps réel des données de production permettent :
- D'optimiser les paramètres de production en fonction des conditions réelles
- De détecter rapidement les dérives de qualité et d'ajuster les processus en conséquence
- D'améliorer la traçabilité des produits tout au long de la chaîne de production
- De faciliter la prise de décision grâce à des tableaux de bord en temps réel
L'adoption de ces technologies nécessite cependant une réflexion approfondie sur la sécurité des données et la formation des équipes. Il est essentiel de mettre en place une stratégie globale de transformation digitale pour tirer pleinement parti des avantages de l'IIoT.